
کوره قوس الکتریکی (به انگلیسی: Electric Arc Furnace) که به صورت مخفف EAF نامیده میشود، کورهای است که مواد فلزی با استفاده از یک قوس الکتریکی در آن، ذوب میشود.
کوره قوس الکتریکی ابزاری پرکاربرد در ذوب قطعات آهنی و غیرآهنی محسوب می شود که با ویژگی هایی چون ایجاد حرارت بسیار زیاد و نرخ تولید بالا در صنایع ذوب ایران و جهان شناخته شده می باشد و در حال حاضر 30 درصد فولادهای جهان با این کوره ها تولید می گردند.
از جمله مواردی که با کوره قوس الکتریکی تولید می شوند شامل ناودانی، میله، تسمه، میلگرد آجدار، طیف وسیعی از گریدهای فولاد، گریدهای میله مورد استفاده در صنعت خودرو و... می باشد.
این کورهها اندازههای متفاوتی داشته و در ایران به دو صورت کورههای قوس الکتریکی سنتی (تخلیه از ناودان) و EBT (تخلیه از کف) استفاده میگردند. دمای ذوب و تخلیه در این کورهها در حدود ۱۶۰۰ درجه و در بعضی از کورههای آزمایشگاهی گاهی دما به ۳۰۰۰ درجه سانتیگراد میرسد.
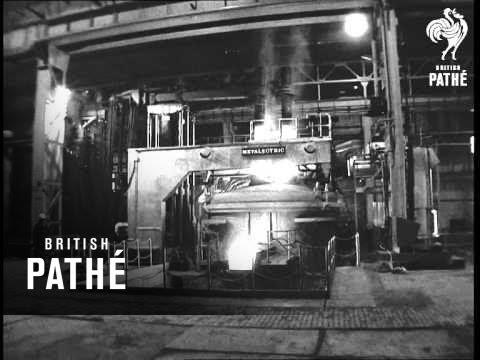
اختراع اولیه کورهٔ قوس الکتریکی بوسیلهٔ آقای همفری دیوی (Humphry Davy) در سال ۱۸۰۸ اتفاق افتاد. اکتشاف آقای دیوی در آن زمان توجه زیادی را به خود جلب کرد، اما این اکتشاف برای چندین سال در حد یک کنجکاوی علمی باقی ماند و هیچکس نتوانست آن را به صورت عملی بهکارگیرد.
اما بالاخره در سال ۱۸۷۸ ارنست ویلیام زیمنس (William Siemens) اولین کوره قوس الکتریکی را ساخت و توانست در یک آزمایش ۲ کیلوگرم آهن قراضه را ظرف ۲۰ دقیقه بوسیله قوس الکتریکی ذوب کند؛ که در آن زمان موفقیت بزرگی بود و در سالهای بعد سبب تحویل چشمگیری در صنعت ذوب آهن شد.
اما در نهایت پل هرویت (Paul Héroult)اولین کورهٔ قوس الکتریکی تجاری را در سال ۱۹۹۰ در شهر لپراز فرانسه ساخت.
کورههای قوس الکتریکی، از طریق ذوب کردن مواد اولیه، توسط قوس الکتریکی ایجاد شده بین الکترودهای گرافیتی و بار فلزی، محصول نهایی را تولید می کنند.
مهمترین مواد اولیه برای تولید فولاد و چدن در کورههای قوس الکتریکی عبارتند از:
- آهن قراضه
- آهن اسفنجی
- شمش چدن کوره بلند
- فرو آلیاژهای آهک و فلورین
در ایران عمدتاً از آهن قراضه و از آهن اسفنجی به صورت گندله یا خشته استفاده میگردد.
در این روش، ابتدا آهن اسفنجی درون کوره قوس الکتریکی ریخته میشود تا ذوب گردد. دمای این کورهها به حدی است که در همان ذوب اولیه، فولاد با درصد کربن نسبتاً پایین تولید میشود. سپس فولاد تولیدشده درون کوره پاتیلی ریخته میشود تا در آنجا عملیات آلیاژسازی انجام شود. این عملیات شامل تنظیم کردن میزان کربن، اضافه کردن عناصر آلیاژی و یکدستسازی ترکیب فولاد است.
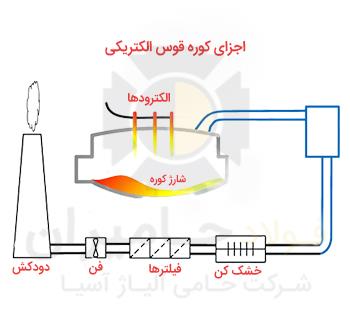
اجزا و ساختمان کورههای قوس الکتریکی
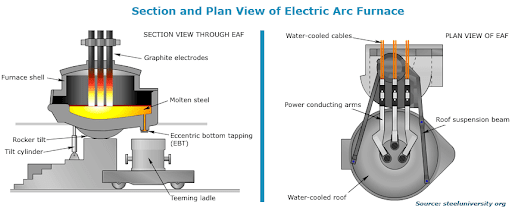
1- بدنهٔ کوره
بهطور کلی بدنهٔ کورههای قوس الکتریکی از سه بخش اصلی تشکیل شدهاست که عبارتاند از: کف یا بوته (heats)، دیوار جانبی (shell) و سقف (roof).
- سقف کوره (roof): به صورت یک کلاهک است و معمولاً به گونهای طراحی میشود که هم سبک باشد و هم استحکام لازم را داشته باشد. در سقف کورههای قوس الکتریکی معمولاً سه سوراخ قرار دارند که این سه منفذ محل عبور الکترودها هستند.معمولاً سقف به گونهای طراحی میشود که همراه با الکتردها قابل حرکت باشند.
- دیوار جانبی کوره (shell): عموماً به صورت استوانهای هستند و با مواد نسوز و همچنین لولههای آبگرد پوشیده شدهاست.
- کف یا بوته کوره (heats): حالت قوسی شکل دارد و برعکس سقف آن عمقش نسبتاً کم و سطح آن زیاد است تا فصل مشترک مذاب با سرباره بیشترین مقدار باشد.
2- الکترودها
کار الکترودها انتقال جریان از بازوهای الکترود به بار کوره از طریق ایجاد قوس الکتریکی میباشد. الکترودهای گرافیتی و زغالی از مهمترین مواد مصرفی در کورههای قوس الکتریکی هستند. این الکترودها تأثیر زیادی در کیفیت مذاب و البته تولید محصول داشته و از نظر اقتصادی نیز سهم قابل توجهی از هزینهها را به خود اختصاص میدهدند. برای تولید مذاب باکیفیت باید از الکترودهای با خواص مشخصی استفاده کرد.
در صنعت معمولاً براساس میزان تولید فولاد و فروآلیاژهای مورد نیاز، از سه نوع الکترود استفاده میشود که به ترتیب عبارتند از:
- الکترودهای زغالی
- الکترودهای گرافیتی
- الکترودهای زینترشده
همانطور که گفته شد در حین عمل ذوب در کوره قوس الکتریکی، الکترودها بهدلایل مختلف از جمله اکسیداسیون، تصعید و شکستگی، از بین میروند. در نتیجه تعویض مرتب الکترودها ضروری میباشد. به همین جهت بخش انتهایی هر یک از الکترودها دارای یک سرپیچ گرد مخروطی شکل است، که داخل آن میتوان یک مغزی پیچ داد. به همین ترتیب الکترودها به یکدیگر پیچ شده و بهطور پیوسته در داخل مذاب مصرف میشوند.
3- تجهیزات الکتریکی
تجهیزات الکتریکی از مهمترین اجزای تشکیل دهندهٔ کورههای قوس الکتریکی میباشد؛ که از سه قسمت زیر تشکیل شدهاست:
- کلید قطع و وصل مدار
- راکتور و ترانسفور ماتور
- تنظیم کنندههای الکترود
- کلید قطع و وصل مدار
فرایند ذوب آهن

برای ذوب و جداسازی مواد و تصفیه از دو روش اسیدی و بازی استفاده میشود.
در روش اسیدی که آستر کوره نیز باید متناسب با آن انتخاب شود، آهن قراضه و مواد خام بایستی درصد گوگرد و فسفر پایین داشته باشند زیرا امکان جدا کردن این مواد در این روش وجود ندارد. هزینه پایین مواد نسوز و دوام بیشتر آسترها و مصرف کمتر انرژی و سیالیت و روانی بیشتر مذاب و سیالیت کم سرباره از مزایای این روش میباشد ولی مصرف قراضههای مخصوص کاربرد آن را بسیار محدود نمودهاست. در این روش مواد شارژ به همراه مقداری مواد کربن زا به کوره ریخته میشود و هیچ نوع مواد سرباره زا به کوره افزوده نمیگردد و پس از عملیات ذوب مقداری ماسه و در مواردی ۱ الی ۳ درصد سنگ آهک به آن میافزایند.
در روش بازی نیز کوره با آستر مناسب بایستی انتخاب گردد روش بازی روشی آسانتر برای ساخت فولاد است و با استفاده از تخلیه سرباره میتوان باعث کاهش گوگرد و فسفرزدایی تا میزان بسیار زیاد گردید و تبدیل نامرغوبترین قراضه به فولاد مرغوب را امکانپذیر میسازد. این روش ممکن است به صورت یک سرباره ای یا دو سرباره ای انجام گیرد.
در مجموع روش بازی مورد استفاده بیشتری دارد و استفاده از مواد سرباره زا چون آهک و روانساز چون آهک و روانساز چون فلوئوراسپار در آن معمول است. در مجتمع فولاد مبارکه اصفهان از این روش استفاده میگردد. معمولاً مرحله شروع ذوب با ولتاژ متوسط قوس الکتریکی آغاز میشود تا از صدمه زدن قوس به سقف جلوگیری شود.
وقتی الکترودها به داخل بار وارد شدند، ولتاژی انتخاب میشود که حداکثر انرژی ورودی را به کوره بدهد. هنگامی که حوضچه مذاب ایجاد شد، میزان ولتاژ را به مقدار متوسط کاهش میدهند تا از آسیب به آسترهای نسوز جلوگیری شود. به محض اینکه سه چهارم بار ذوب شد یا حوضچه فرورفت، روش معمول این است که الکترودها را بالا میکشند و قراضههای گداخته شده باقیمانده را که در قسمتهای دیگر کوره موجودند، با هم مخلوط می کنند.
برای کسب اطلاعات بیشتر در زمینه انواع آهن آلات و فولاد به وبسایت فولاد حامیران مراجعه نمایید:
از همراهی شما سپاسگزاریم.
منتظر نظرات تخصصی شما هستیم.