کمپرسور پیستونی
کمپرسور پیستونی یک کمپرسور با جابجایی مثبت است که از پیستون های هدایت شده توسط میل لنگ برای انتقال گازها در فشار بالا استفاده می کند.
گاز ورودی وارد منیفولد مکش می شود، سپس به داخل استوانه فشرده سازی جریان می یابد و در آنجا توسط پیستونی که از طریق میل لنگ در حرکت رفت و برگشتی فشرده شده و سپس تخلیه می شود. برنامه های کاربردی شامل پالایشگاه های نفت، خطوط لوله گاز، کارخانه های شیمیایی، کارخانه های پردازش گاز طبیعی، تهویه مطبوع و کارخانه های تبرید است. یکی از کاربردهای ویژه، دمیدن بطری های پلاستیکی ساخته شده از پلی اتیلن ترفتالات (PET) است.
در کمپرسور پیستونی مایع یونی بسیاری از مهر و موم ها و یاطاقان ها در طرح حذف شدند زیرا مایع یونی با گاز مخلوط نمی شود. عمر مفید حدود 10 برابر بیشتر از یک کمپرسور معمولی دیافراگم با کاهش نگهداری در حین استفاده است، هزینه های انرژی تا 20 درصد کاهش می یابد. مبدلهای حرارتی که در یک کمپرسور پیستونی معمولی استفاده می شوند، با خروج گرما در خود سیلندر جایی که تولید می شود، حذف می شوند. تقریباً 100 of از انرژی وارد شده به فرایند با انرژی کمی که به عنوان گرمای پسماند هدر می رود، مصرف می شود.
کمپرسور رفت و برگشتی یک ماشین با جابجایی مثبت است که از یک پیستون برای فشرده سازی گاز و رساندن آن در فشار بالا استفاده می کند.
آنها اغلب یکی از مهمترین و گرانترین سیستمهای تأسیسات تولیدی هستند و شایسته توجه ویژه هستند. خطوط انتقال گاز، کارخانه های پتروشیمی، پالایشگاه ها و بسیاری از صنایع دیگر همگی به این نوع تجهیزات وابسته هستند.
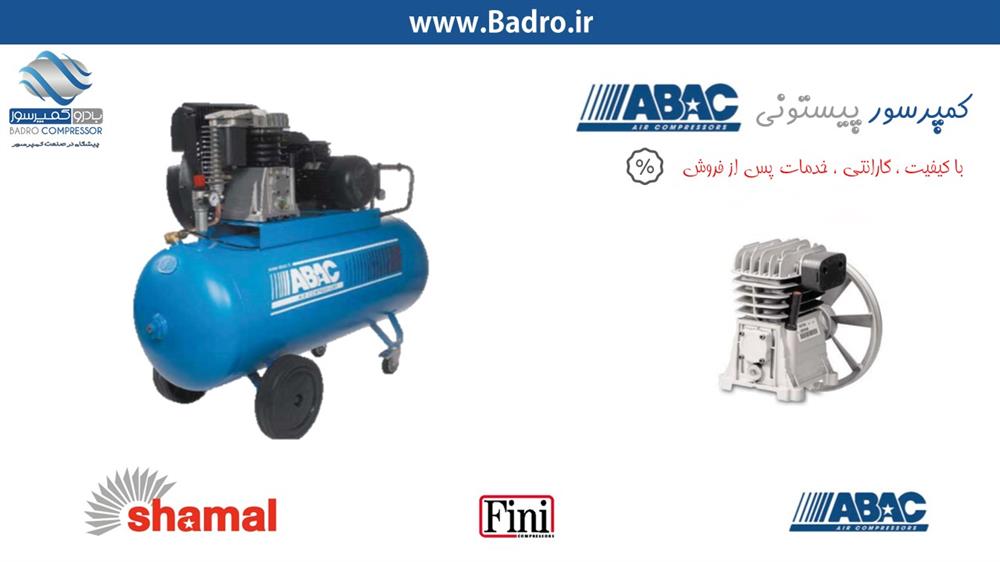
با توجه به عوامل متعدد، از جمله کیفیت طرح یا مشخصات اولیه، کفایت شیوه های نگهداری و عوامل عملیاتی، تاسیسات صنعتی می توانند هزینه های چرخه عمر و قابلیت اطمینان متفاوتی را از تاسیسات خود انتظار داشته باشند.
تقریباً در همه تاسیسات صنعتی کمپرسورهای مختلفی یافت می شود. انواع گازهای فشرده شامل موارد زیر است:
- هوا برای سیستم های هوای ابزار فشرده و ابزار
- هیدروژن، اکسیژن و غیره برای پردازش شیمیایی
- کسرهای سبک هیدروکربنی در تصفیه
- گازهای مختلف برای ذخیره یا انتقال
- برنامه های کاربردی دیگر
دو دسته اصلی کمپرسورهای صنعتی وجود دارد: جریان متناوب (جابجایی مثبت)، شامل انواع رفت و برگشتی و دوار و جریان مداوم ، از جمله انواع جریان گریز از مرکز و محوری.
کمپرسورهای رفت و برگشتی معمولاً در مواردی استفاده می شوند که نسبت فشرده سازی بالا (نسبت تخلیه به فشار مکش) در هر مرحله بدون سرعت جریان بالا مورد نیاز است و سیال فرآیند نسبتاً خشک است.
کمپرسورهای گاز مرطوب از انواع گریز از مرکز هستند. جریانهای بالا و نسبتهای فشرده سازی کم بهتر است توسط کمپرسورهای جریان محوری ارائه شوند. انواع روتاری در درجه اول در برنامه های هوای فشرده مشخص می شوند، اگرچه انواع دیگر کمپرسورها نیز در سرویس هوایی یافت می شوند.
اکثر طراحی تجهیزات شامل سیستم های روغن کاری بلوکی و تغذیه نیرویی می باشد. اما وقتی تحمل فرآیند برای انتقال نفت صفر باشد، از طرح های بدون روغن استفاده می شود.
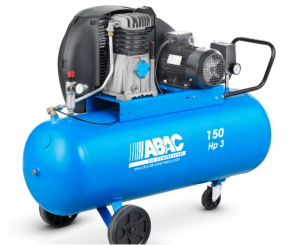
سیلندرها برای کاربردهای بزرگتر (قطع معمولی 300 اسب بخار) مجهز به مجاری خنک کننده برای ترموسیفون یا سیستم های خنک کننده مایع در گردش هستند ، در حالی که برخی از کمپرسورهای کوچکتر خانگی و مغازه ای معمولاً با هوا خنک می شوند. سیلندرهای کاربردی بزرگ عموماً دارای آسترهای قابل تعویض هستند که با فشار به داخل سوراخ نصب شده اند و ممکن است شامل پین ضد چرخش باشند.
گاز فرآیند به داخل سیلندر کشیده می شود، فشرده می شود، محفظه می شود و سپس توسط دریچه های مکانیکی که معمولاً به طور خودکار با فشارهای افتراقی عمل می کنند، رها می شود. بسته به طراحی سیستم ، سیلندرها ممکن است دارای یک یا چند سوپاپ مکش و تخلیه باشند.
تخلیه کننده ها و جیب های ترخیص دریچه های مخصوصی هستند که درصد بار کامل حمل شده توسط کمپرسور را با سرعت چرخشی معین درایور آن کنترل می کنند. تخلیه کننده ها عمل سوپاپ های مکش را دستکاری می کنند تا گاز بازیافت شود.
شیرهای جیبی ترخیص کننده فضای سر سیلندر (حجم ترخیص) را تغییر می دهند. ممکن است حجم آنها ثابت یا متغیر باشد. این دستگاه ها خارج از حوصله این مقاله هستند.
قطعه فاصله (گاهی اوقات سگ سگ نامیده می شود) یک عضو ساختاری است که قاب کمپرسور را به سیلندر متصل می کند. از اختلاط مایعات بین استوانه و قطعه فاصله باید اجتناب شود. حلقه های بسته بندی حاوی فشار گاز در داخل سیلندر هستند و با پاک کردن روغن از میله پیستون در طول مسیر ، از ورود روغن به سیلندر جلوگیری می کنند.
قطعه فاصله معمولاً با توجه به خطرناک ترین مواد موجود در سیستم ، که اغلب گاز فشرده شده در سیلندر است ، تخلیه می شود. حلقه های بسته بندی طوری طراحی شده اند که حاوی گاز درون سیلندر باشند ، اما با فشار زیاد ممکن است قسمتی از گاز فشرده از حلقه های بسته بندی نشت کند.
چرخ دنده، که در چارچوب کمپرسور قرار دارد ،شامل سربرگ و میله اتصال است که میله پیستون را به میل لنگ متصل می کند و حرکت چرخشی آن را به حرکت خطی رفت و برگشتی تبدیل می کند.
میل لنگ مجهز به وزنه های متقابل است تا نیروهای دینامیکی ایجاد شده توسط حرکت پیستون های سنگین را متعادل کند. در چارچوب کمپرسور توسط یاتاقانهای ساده در چندین مجله پشتیبانی می شود. یک چرخ فلک نیز برای ذخیره اینرسی چرخشی و ارائه مزیت مکانیکی برای چرخش دستی مجموعه ارائه شده است.
برخی از کمپرسورها با استفاده از یک پمپ روغن یکپارچه و محور محور، چرخ دنده های فریم خود را روغن کاری می کنند، در حالی که برخی دیگر دارای سیستم های روانکاری گسترده تر و مجهز به لغزش هستند. تمام سیستمهای طراحی شده مناسب نه تنها گردش روغن را در سطوح مهم تجهیزات، بلکه کنترل دما، فیلتراسیون و برخی ابزارهای اندازه گیری و افزونگی را نیز انجام می دهند.
گازهای مکش عموماً از طریق صافی ها و جداکننده های مکنده عبور می کنند تا ذرات درگیر، رطوبت و سیال مرحله مایع را که می تواند آسیب جدی به دریچه های کمپرسور و سایر اجزای حیاتی وارد کند، منتقل کرده و حتی یکپارچگی سیلندر را با پیامدهای فاجعه آمیز تهدید کند.
گاز همچنین ممکن است پیش گرم شود تا گاز فرآیند مایع به فاز بخار منتقل شود. Intercoolers فرصتی برای حذف گرما از گاز فرآیند بین مراحل فشرده سازی فراهم می کند. (بخش زیر را ببینید: چرخه ترمودینامیکی.) این مبدل های حرارتی ممکن است بخشی از سیستم (های) خنک کننده روغن و/یا سیلندر کمپرسور باشند یا به سیستم آب خنک کننده کارخانه متصل شوند.
در سمت تخلیه ، مخازن تحت فشار به عنوان میراکننده ضربان عمل می کنند و ظرفیت سیستم را برای برابر کردن جریان و فشارهای مربوط به ضربات فشاری پیستون فراهم می کنند.
به طور معمول ، کمپرسورهای رفت و برگشتی دستگاه های نسبتاً کم سرعت هستند و توسط یک موتور الکتریکی مستقیم یا کمربند ، با یا بدون کنترل کننده درایو سرعت متغیر ، حرکت می کنند.
اغلب موتور به صورت جدایی ناپذیر کمپرسور ساخته می شود و محور موتور و میل لنگ کمپرسور یک تکه هستند و نیازی به اتصال ندارند. از کاهنده های سرعت گیربکس در تاسیسات مختلف استفاده می شود.
گاهی اوقات، هرچند کمتر، توسط توربین های بخار یا منابع دیگر قدرت مانند گاز طبیعی یا موتورهای دیزلی هدایت می شوند. طراحی کلی سیستم و نوع راننده انتخاب شده بر روانکاری این سیستم های جانبی تأثیر می گذارد.
چرخه ترمودینامیکی
توضیح چند اصل اساسی ترمودینامیکی برای درک علم کمپرسورهای رفت و برگشتی ضروری است. فشرده سازی درون سیلندر به صورت یک چرخه چهار قسمتی رخ می دهد که با هر پیشروی و عقب نشینی پیستون (دو ضربه در هر چرخه) رخ می دهد.
چهار قسمت چرخه عبارتند از فشرده سازی ، تخلیه ، انبساط و جذب. آنها به صورت گرافیکی با فشار در مقابل حجم نشان داده شده اند که در نمودار P-V معروف است.
منبع: بادرو کمپرسور